5.6 Maintaining site safety
Maintaining site safety on a construction project, such as an ADU build, is crucial for protecting workers, preventing accidents, and ensuring compliance with Occupational Safety and Health Administration (OSHA) regulations. Implementing best practices for safety and adhering to OSHA guidelines not only reduces the risk of injuries but also minimizes potential project delays, legal liabilities, and financial penalties.
Why It Matters:
Site safety protects workers, prevents accidents, and ensures compliance with OSHA regulations, avoiding delays, legal issues, and penalties.
Key Topics:
- OSHA Compliance: Understanding key regulations like fall protection, scaffolding, and hazard communication.
- Safety Best Practices: Developing safety plans, regular training, proper PPE use, and emergency preparedness.
- Focused Areas: Fall protection, electrical safety, trenching, and site organization to prevent common hazards.
- Inspections: Regular audits to ensure ongoing safety and compliance.
1. Overview of OSHA Regulations
OSHA is the primary federal agency responsible for enforcing workplace safety and health standards. OSHA regulations require construction employers to provide a safe working environment by identifying and mitigating hazards.
Key OSHA regulations that apply to construction sites include:
- 29 CFR Part 1926: The primary set of OSHA safety and health standards for the construction industry.
- General Duty Clause: Employers must provide a workplace free from recognized hazards that are causing or likely to cause death or serious harm.
Common OSHA Regulations for Construction:
- Fall Protection: Employers must provide protection for workers working at heights of 6 feet or more.
- Scaffolding: Scaffolds must be designed, erected, and maintained according to OSHA standards.
- Hazard Communication: Employers must inform workers of hazardous chemicals in the workplace through labeling, safety data sheets (SDS), and training.
- Personal Protective Equipment (PPE): Employers must provide appropriate PPE (e.g., hard hats, safety glasses, gloves) based on site-specific hazards.
- Electrical Safety: Electrical hazards must be controlled through proper equipment grounding, lockout/tagout procedures, and protective measures around live wires.
2. Best Practices for Maintaining Site Safety
a. Develop a Site Safety Plan
A comprehensive Site Safety Plan should outline all potential hazards, the required safety measures, and emergency procedures. The plan should cover:
- Hazard Identification: Assess the site for risks related to falls, electrical hazards, excavation, heavy equipment, etc.
- Preventive Measures: Detail safety protocols, such as the use of fall protection systems, proper handling of hazardous materials, and PPE requirements.
- Emergency Response: Outline evacuation procedures, first-aid protocols, and contacts for emergency services.
b. Conduct Regular Safety Training
Workers must be educated about safety procedures, proper use of equipment, and specific hazards they may encounter on the job. OSHA requires training for certain high-risk tasks such as:
- Fall Protection: Training on the proper use of safety harnesses, guardrails, and fall arrest systems.
- Scaffolding Safety: Training on the erection, dismantling, and safe use of scaffolds.
- Hazard Communication: Workers must be trained on how to read labels and safety data sheets (SDS) for hazardous chemicals.
Training should be refreshed regularly and updated whenever new equipment or hazards are introduced to the site.
c. Personal Protective Equipment (PPE)
Ensure all workers are equipped with appropriate PPE based on the hazards present on-site. This may include:
- Hard Hats: Required for protection from falling objects or head injuries.
- Safety Glasses/Goggles: Protection from flying debris, dust, or chemicals.
- Gloves: Choose the appropriate type of gloves (e.g., cut-resistant, heat-resistant, chemical-resistant) for the task at hand.
- Fall Protection: Workers operating at heights must wear harnesses connected to lifelines or fall arrest systems.
- Hearing Protection: Use earplugs or earmuffs in areas where noise levels exceed OSHA’s permissible exposure limits.
3. Fall Protection: Reducing the Risk of Falls
Falls are one of the leading causes of injuries and fatalities in construction. OSHA requires employers to provide fall protection for employees working at heights of 6 feet or more.
Key Fall Protection Measures:
- Guardrails: Install guardrails around open sides, edges, and holes that workers could fall through.
- Personal Fall Arrest Systems (PFAS): Workers exposed to fall hazards should be equipped with a PFAS, which includes a harness, lanyard, and anchor points.
- Ladders and Scaffolds: Ladders and scaffolds must be stable, secure, and meet OSHA standards. Scaffolds should be equipped with guardrails and toe boards.
- Training: Workers must be trained in the proper use of fall protection equipment and the specific risks associated with working at heights.
4. Electrical Safety
Electrical hazards are common on construction sites and can result in serious injury or death. OSHA mandates strict safety protocols to protect workers from electrical shocks, burns, and electrocution.
Key Electrical Safety Practices:
- Lockout/Tagout: Establish lockout/tagout procedures to ensure that equipment is de-energized and cannot be powered on during maintenance or repair.
- Grounding: Ensure that all electrical tools and systems are properly grounded to prevent accidental shocks.
- GFCI Protection: Ground-fault circuit interrupters (GFCIs) must be installed on all temporary power sources to prevent electrical shock hazards.
- Overhead Power Lines: Workers should maintain a safe distance from overhead power lines, using barriers or warning signs if necessary.
5. Scaffolding Safety
Scaffolding poses significant risks when improperly erected or used. OSHA requires scaffolding to be designed and installed according to strict guidelines.
Scaffolding Safety Requirements:
- Inspection: Scaffolds must be inspected daily by a competent person to ensure they are safe for use.
- Load Capacity: Ensure that scaffolds are designed to hold at least four times their maximum intended load.
- Guardrails and Fall Protection: Scaffolds higher than 10 feet must have guardrails and mid-rails to prevent falls.
- Safe Access: Workers should have safe access to the scaffold using ladders, stair towers, or ramps.
6. Hazard Communication
OSHA’s Hazard Communication Standard (HCS) requires employers to inform and train workers about hazardous chemicals they may encounter on-site.
Key Hazard Communication Practices:
- Labels: Ensure all hazardous materials are properly labeled with information on the substance and its associated risks.
- Safety Data Sheets (SDS): Maintain accessible SDS for every hazardous chemical on-site. Workers should know how to interpret the information in these sheets.
- Training: Provide training on how to handle hazardous chemicals safely, including appropriate PPE and emergency procedures in case of spills or exposure.
7. Excavation and Trenching Safety
Excavation and trenching activities can result in cave-ins, which are one of the most dangerous hazards on a construction site. OSHA has strict regulations for trench safety.
Excavation Safety Practices:
- Trench Protection Systems: Trenches 5 feet or deeper require a protective system, such as trench boxes, shoring, or sloping.
- Competent Person: A competent person must inspect trenches daily to identify and correct any hazards.
- Access and Egress: Trenches deeper than 4 feet must have safe exit points (ladders or ramps) within 25 feet of workers.
- Soil Classification: Test soil conditions to determine the appropriate trench protection system.
8. Site Organization and Housekeeping
A well-organized construction site reduces the risk of accidents, such as slips, trips, and falls. Good housekeeping involves keeping the site clean, free from clutter, and properly organized.
Best Practices for Site Organization:
- Clear Pathways: Keep pathways, walkways, and work areas free from debris, tools, and materials.
- Tool Storage: Store tools and equipment in designated areas when not in use to prevent trips and injuries.
- Material Stacking: Store and stack materials safely to prevent tipping or shifting.
- Waste Management: Dispose of waste materials promptly and safely, especially hazardous waste.
9. Emergency Preparedness
Being prepared for emergencies is critical to minimizing injuries and ensuring a swift response to accidents or hazards on-site.
Emergency Procedures:
- First Aid: Ensure first-aid kits are available and easily accessible. Train workers on basic first-aid procedures, including how to respond to common construction injuries (e.g., cuts, falls, burns).
- Emergency Exits: Clearly mark emergency exits and ensure they are free from obstructions.
- Fire Prevention: Install fire extinguishers throughout the site, especially near flammable materials. Train workers on fire safety and how to use extinguishers.
- Evacuation Plan: Develop an evacuation plan and communicate it to all workers. Conduct regular emergency drills.
10. Regular Safety Audits and Inspections
To ensure ongoing compliance with OSHA regulations, conduct regular safety audits and inspections of the job site. Inspections help identify potential hazards before they cause accidents.
Inspection Checklist:
- Check fall protection systems, scaffolds, and ladders.
- Ensure PPE is being worn properly by all workers.
- Inspect electrical systems, tools, and equipment for safety hazards.
- Verify that all materials and chemicals are labeled and stored properly.
Conclusion
Maintaining safety on a construction site involves careful planning, continuous education, and adherence to OSHA standards. By developing a strong safety culture, providing the necessary training, ensuring the use of proper equipment and PPE, and conducting regular inspections, you can prevent accidents and maintain a safe working environment for your team.
By following these best practices for OSHA compliance and hazard prevention, you'll protect both your workers and your ADU construction project from costly delays, injuries, and
Up next
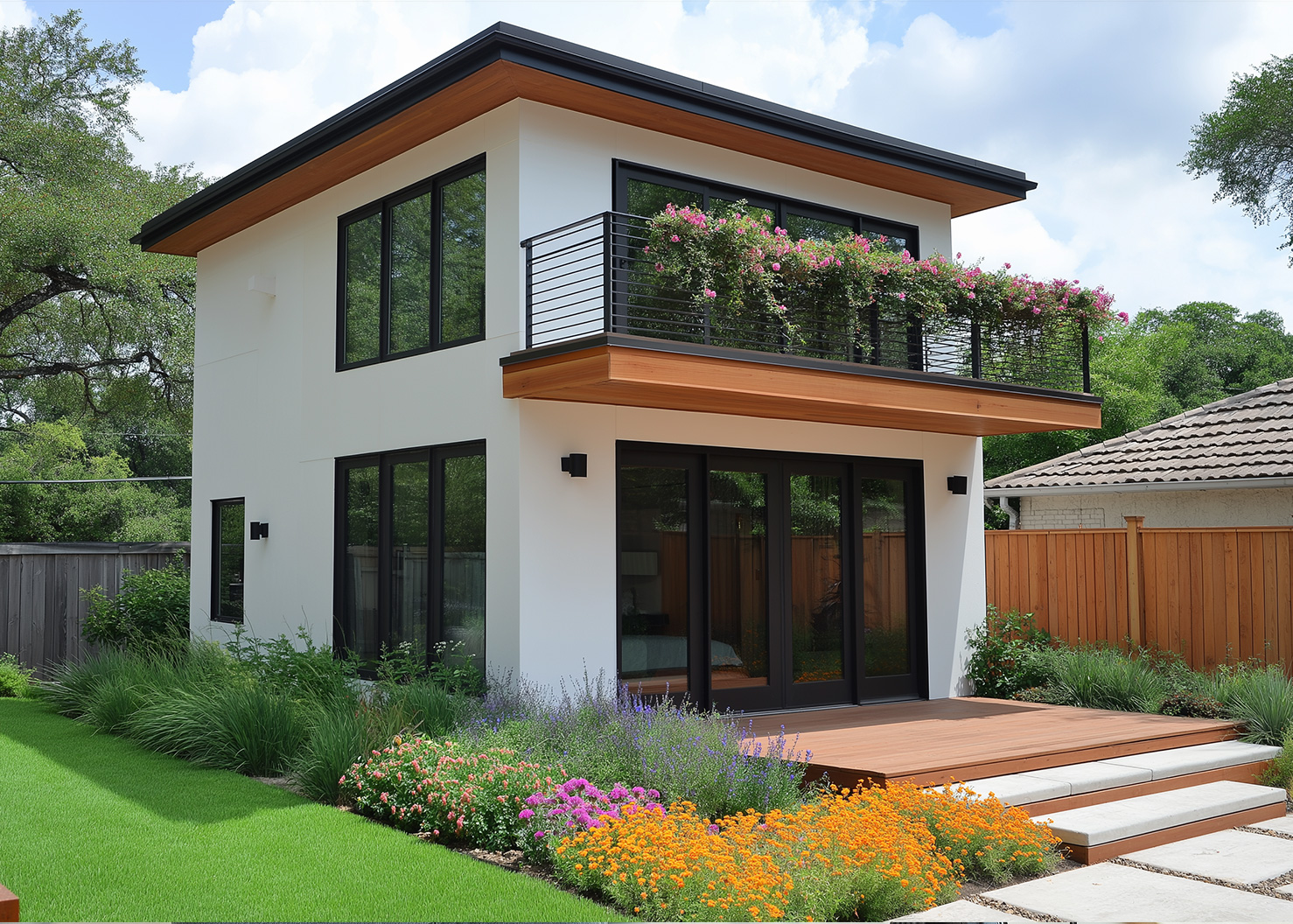