5.1.4 Rough Ins
Rough-in systems refer to the installation of the basic framework for plumbing, electrical, and HVAC (Heating, Ventilation, and Air Conditioning) before walls, insulation, and other finishes are applied. These systems are crucial for the functionality and safety of the ADU (Accessory Dwelling Unit) and must comply with local building codes. Here's a detailed breakdown of each rough-in system:
Why It Matters
The rough-in phase sets the framework for plumbing, electrical, and HVAC systems before walls are finished. Proper installation during this stage ensures functionality, safety, and compliance with building codes, laying the foundation for a well-operating ADU.
Key Systems and Steps
- Plumbing Rough-In
- Installation: Water supply lines (PEX or copper), drain, waste, and vent pipes (PVC or ABS).
- Key Details: Pressure test water lines, ensure proper slope for drains (¼ inch per foot), and vent to prevent sewer gases.
- Cost: $1,500–$5,000 depending on complexity and materials.
- Electrical Rough-In
- Installation: Wiring for outlets, switches, and appliances; grounding; and placement of electrical boxes.
- Key Details: Use GFCI outlets in wet areas, ensure proper wire gauges, and install hardwired smoke and carbon monoxide detectors.
- Cost: $1,500–$4,000 depending on size and requirements.
- HVAC Rough-In
- Installation: Ductwork, vents, and HVAC equipment (furnace, air handler, or mini-split systems).
- Key Details: Properly size ducts for airflow, seal duct joints, and vent exhaust systems to the exterior.
- Cost: $2,000–$6,000 based on system type and complexity.
Inspection and Testing
- Plumbing: Check slopes, pressure-test water lines, and inspect venting.
- Electrical: Ensure grounding, code-compliant wiring, and proper GFCI installation.
- HVAC: Inspect duct sizing, sealing, and ventilation systems.
Common Issues to Avoid
- Plumbing: Incorrect pipe slopes, unsupported pipes, or improper venting.
- Electrical: Overcrowded boxes, inconsistent wire gauges, or missing GFCI outlets.
- HVAC: Poor duct sealing, inadequate return vents, or improper exhaust venting.
1. Plumbing Rough-In
The plumbing rough-in stage involves installing the water supply lines, drain pipes, vent pipes, and fixture supports before the walls and floors are finished. This stage ensures that all pipes are correctly positioned for sinks, toilets, showers, and other fixtures.
Plumbing Rough-In Steps:
- Water Supply Lines: Install cold and hot water supply lines using materials such as PEX (cross-linked polyethylene) or copper pipes. PEX is more commonly used in modern construction due to its flexibility, cost-effectiveness, and ease of installation.some text
- Water Line Sizes: Water lines are typically ½ inch or ¾ inch in diameter.
- Pressure Testing: Once the lines are installed, they must be pressure-tested to ensure there are no leaks before closing up the walls.
- Drainage and Venting Systems: Install drain, waste, and vent (DWV) pipes that allow for proper drainage and ventilation of wastewater. PVC (Polyvinyl Chloride) or ABS (Acrylonitrile Butadiene Styrene) pipes are commonly used for drain lines.some text
- Sloping Pipes: Drain lines should slope downward at ¼ inch per foot to ensure proper drainage.
- Vent Pipes: Venting is required to prevent sewer gases from entering the ADU and to allow air to enter the drainage system, ensuring smooth flow.
- Fixture Locations: Stub out the pipes for sinks, toilets, showers, and other plumbing fixtures according to the design plan.
- Water Heater Rough-In: If installing a water heater, the rough-in includes the positioning of water lines and gas/electrical connections (depending on whether it's gas or electric).
Typical Costs:
- Plumbing rough-in costs generally range from $1,500 to $5,000 depending on the complexity of the project, materials used, and regional labor rates.
2. Electrical Rough-In
The electrical rough-in involves installing all wiring, electrical boxes, and conduit before the insulation and drywall are added. Proper electrical rough-in is essential for providing power, lighting, and appliance connections throughout the ADU.
Electrical Rough-In Steps:
- Running Electrical Wires: Install wiring through the framing for all outlets, switches, and light fixtures. Most residential electrical systems use 12-gauge or 14-gauge wire for standard circuits.some text
- Dedicated Circuits: Larger appliances (e.g., water heaters, stoves, or HVAC systems) require dedicated circuits with heavier-gauge wire, typically 10-gauge for 30-amp circuits.
- Service Panel: Connect wiring to the main electrical panel (breaker box), ensuring enough capacity for the ADU’s electrical needs.
- Outlet and Switch Boxes: Position electrical boxes where outlets, switches, and light fixtures will be located, ensuring the boxes are level and securely attached to studs.some text
- Code Requirements: Outlets should generally be placed no more than 12 feet apart, with outlets within 6 feet of each door and no more than 4 feet from any kitchen counter.
- Grounding and Safety: Install ground wires and ensure the entire electrical system is properly grounded to avoid electrical hazards. In areas where moisture is present (e.g., bathrooms or kitchens), GFCI (Ground Fault Circuit Interrupter) outlets must be used for safety.
- Smoke Detectors and Carbon Monoxide Detectors: These life safety devices must be installed during the rough-in phase, and hardwired detectors with battery backup are typically required.
Typical Costs:
- Electrical rough-in for an ADU usually costs between $1,500 and $4,000, depending on the size of the ADU, local building codes, and the complexity of the electrical system.
3. HVAC Rough-In
The HVAC rough-in involves the installation of ductwork, venting, and system components that will regulate heating, cooling, and ventilation in the ADU. This includes positioning the furnace or air handler, running ducts, and preparing for thermostat placement.
HVAC Rough-In Steps:
- Ductwork Installation: Install ducts that will carry conditioned air to and from the living spaces. These include supply ducts (bringing conditioned air to rooms) and return ducts (drawing air back to the system).some text
- Duct Sizing: Ensure ducts are sized properly based on the HVAC system’s capacity to maintain efficient airflow throughout the ADU.
- Duct Material: Most residential HVAC systems use sheet metal or flexible ductwork depending on space constraints and efficiency needs.
- Air Registers and Returns: Install supply and return air vents in each room to ensure balanced air circulation.some text
- Air Flow Calculations: The number and size of registers should be based on air flow calculations to ensure consistent temperature control in all areas.
- HVAC Equipment Placement: Position the furnace, air handler, or heat pump unit (for electric systems), ensuring they are installed in an accessible location for future maintenance.some text
- Mini-Split Systems: For smaller ADUs, mini-split ductless systems are often a cost-effective and energy-efficient choice, requiring only a small refrigerant line and electrical connection.
- Ventilation and Exhaust: Install venting for bathroom fans, kitchen exhaust fans, and laundry rooms to ensure proper ventilation. Make sure venting extends to the exterior of the building to remove excess moisture and odors.
Typical Costs:
- HVAC rough-in costs for an ADU typically range from $2,000 to $6,000, depending on the size of the system, the complexity of the ductwork, and the type of system (e.g., mini-split, forced air, or radiant heat).
Inspection and Testing
After completing the rough-in phase for plumbing, electrical, and HVAC systems, inspections are required before closing up walls with insulation and drywall. Inspectors will verify that all systems are installed to code and test for functionality.
- Plumbing Inspection: Tests include pressure testing the water lines and checking that drain lines are correctly sloped and vented.
- Electrical Inspection: Inspectors will check wire gauges, grounding, and GFCI outlets and ensure all electrical boxes are installed correctly.
- HVAC Inspection: Ductwork will be inspected for proper installation, and the HVAC system may be tested to ensure airflow and efficiency.
Conclusion
The rough-in stage is critical to the success of the entire ADU project, as it lays the foundation for plumbing, electrical, and HVAC systems that will serve the structure for years to come. Each system has specific requirements for installation, testing, and code compliance to ensure the ADU is safe, functional, and energy-efficient.
During inspections for construction projects, including ADUs, certain common issues often arise that can delay progress, require costly fixes, or fail code requirements. These issues typically occur in the rough-in stages of plumbing, electrical, HVAC, and structural framing. Below are some of the most common inspection issues across these systems:
1. Plumbing Inspection Issues
- Incorrect Slope for Drain Lines: Drain pipes need to slope properly (usually ¼ inch per foot) to ensure proper drainage. A slope that’s too steep or too shallow can cause blockages or poor drainage.
- Unvented or Improperly Vented Drains: Vents allow air to enter the drain lines and prevent suction, which helps water flow smoothly. Missing or incorrectly installed vent pipes can lead to slow drainage and sewer gas entering the ADU.
- Unsupported PEX or PVC Pipes: Plumbing pipes must be properly supported to prevent sagging, leaks, or future damage. Inspections often fail if the support spacing is too wide.
- Incorrect Pipe Sizes: Using the wrong size pipes for water supply lines or drainage can cause performance issues. For example, using a ½-inch pipe instead of a ¾-inch pipe for main water lines can restrict water flow.
2. Electrical Inspection Issues
- Improper Grounding: Failure to correctly ground electrical circuits and outlets is a common problem. This can lead to shock hazards and code violations. Electrical systems need proper grounding rods, and each circuit should be correctly bonded to the ground.
- Missing GFCI Outlets: Ground Fault Circuit Interrupter (GFCI) outlets are required in areas with moisture, such as kitchens, bathrooms, and exterior locations. Missing or incorrectly wired GFCI outlets are common inspection issues.
- Overcrowded Electrical Boxes: Each electrical box has a maximum number of wires it can safely accommodate based on its size. Overcrowding these boxes is a frequent code violation.
- Improper Wire Splicing: All wire splices must be made inside an approved junction box with proper wire nuts or connectors. Uncovered or incorrectly spliced wires are a major safety hazard.
- Inconsistent Wire Gauges: Using mismatched wire gauges in a single circuit can lead to overheating and electrical failure. For instance, using 12-gauge wire for some outlets and 14-gauge for others on the same circuit is a common error.
3. HVAC Inspection Issues
- Improper Duct Sizing: Ductwork that is too small for the HVAC system can restrict airflow, leading to inefficient heating or cooling. Proper calculations are required to size ducts correctly based on the ADU’s square footage and system output.
- Inadequate Return Air Vents: If there aren’t enough return air vents in the system, it can cause uneven heating and cooling, increasing the system's load and reducing efficiency.
- Poor Duct Sealing: Duct leaks or improperly sealed joints can cause a significant loss of conditioned air, leading to inefficient HVAC operation and higher energy costs.
- Improper Venting of Exhaust Systems: Bathroom and kitchen exhaust fans must vent to the outside. Venting into an attic or crawlspace is a common violation, leading to moisture issues and potential mold growth.
4. Structural and Framing Inspection Issues
- Improper Stud Spacing: Framing studs need to be spaced according to local codes, typically 16 or 24 inches on center. Incorrect spacing weakens the structural integrity of the walls and can lead to failing the inspection.
- Missing Fire Blocking: Fire blocking is required in certain framing areas to prevent the spread of fire within wall cavities. Missing or improperly installed fire blocking is a common issue.
- Poor Load Distribution: Load-bearing walls must be framed properly to support the structure above. Incorrectly framed walls or missing headers over doors and windows can cause structural issues.
- Nailing Pattern Violations: Inspectors often find framing issues related to incorrect or insufficient nailing patterns. Building codes specify the number of nails required to attach sheathing or framing components.
5. General Building Code Violations
- Failure to Follow Plans: Deviations from the approved construction plans without getting amendments approved by local authorities can result in inspection failures. All changes must be documented and resubmitted if needed.
- Lack of Accessibility Features: For structures that require compliance with ADA or local accessibility guidelines, missing or incorrectly installed accessibility features, such as ramps, door widths, or grab bars, can cause inspection failures.
- Incomplete Work: Inspections can fail if parts of the rough-in system or framing are incomplete, such as missing wall sheathing or incomplete ductwork.
6. Documentation and Permit Issues
- Missing or Incorrect Permits: Failing to acquire the necessary permits or providing incomplete documentation can result in delays or fines. Building officials may halt work until the correct paperwork is submitted.
- Skipping Required Inspections: Some builders may neglect to schedule required inspections for various phases of construction, such as foundation or rough-in inspections, which can lead to delays or rework.
Conclusion
Common inspection issues in ADU construction include problems related to plumbing, electrical, HVAC, and framing. These issues often stem from improper installation, deviations from code, or failure to follow approved plans. Avoiding these common pitfalls by working with licensed contractors, adhering to local codes, and conducting internal quality checks can help you pass inspections more easily and avoid costly delays.
Sources:
- HomeAdvisor: Common Building Code Violations
- The Spruce: Inspection Failures
- International Code Council (ICC) Building Inspections
Tip: Ensure all systems are inspected before closing up the walls to avoid costly adjustments later.
Up next
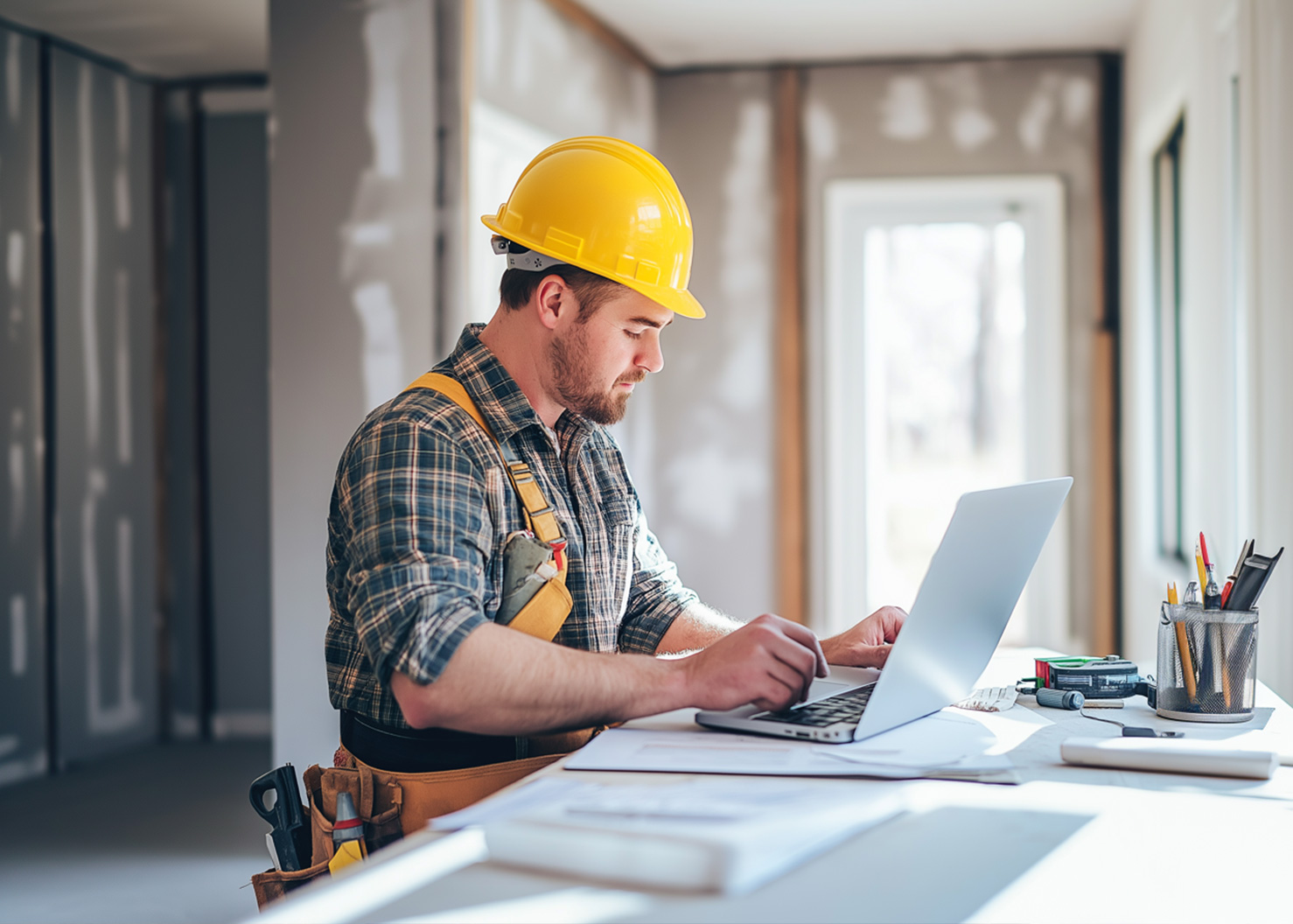