5.4: Managing Subcontractors
Managing subcontractors effectively is essential for a successful ADU construction project, especially for specialized tasks like electrical, plumbing, and HVAC work. Proper selection, vetting, and ongoing management ensure that the project runs smoothly, on schedule, and within budget. Here’s a detailed guide on how to select, vet, and manage subcontractors for specific tasks:
Why It Matters
Effectively managing subcontractors is crucial for maintaining project timelines, ensuring quality, and controlling costs in ADU construction. A well-organized approach fosters clear communication, accountability, and collaboration among all parties involved.
Key Components
- Selecting the Right Subcontractors
- Qualifications: Verify licenses, certifications, and experience relevant to ADU projects.
- References: Check reviews, past work, and client testimonials.
- Bids and Estimates: Compare quotes for labor and materials to balance quality and budget.
- Defining Roles and Expectations
- Contracts: Provide clear agreements outlining scope of work, timelines, and payment terms.
- Deliverables: Specify milestones and the quality standards expected at each stage.
- Communication: Establish preferred communication channels and regular check-ins.
- Scheduling and Coordination
- Project Timeline: Create a detailed schedule to avoid overlaps or delays in tasks (e.g., plumbing before drywall installation).
- Dependencies: Coordinate interdependent tasks to ensure seamless workflow among subcontractors.
- Flexibility: Account for unforeseen delays or adjustments in the timeline.
- Quality Assurance and Inspections
- Site Visits: Conduct regular inspections during and after subcontractors’ work.
- Compliance: Ensure adherence to local codes and project specifications.
- Feedback: Provide constructive feedback to maintain high standards and address issues early.
- Managing Payments
- Milestone Payments: Link payments to completed project phases or deliverables.
- Lien Releases: Collect signed lien waivers with payments to protect against future claims.
- Retention: Hold a portion of payment until final inspections are passed.
- Handling Disputes
- Conflict Resolution: Address disputes promptly through clear documentation and open communication.
- Contracts: Refer to terms for resolution methods, such as mediation or arbitration.
Toolbox Ideas
- Subcontractor Agreement Template
- A customizable contract template covering roles, payment terms, and project scope.
- Project Schedule Template
- A tool to plan and track subcontractor tasks and deadlines.
- Quality Assurance Checklist
- A step-by-step guide for inspecting subcontractor work and ensuring compliance.
- Subcontractor Questions
1. Selection of Subcontractors
a. Identify Project Needs
First, determine the scope of work and the specialized trades required for your project. Common subcontractors for an ADU build include:
- Electricians: For wiring, outlet installations, lighting, and other electrical needs.
- Plumbers: For water supply, drain systems, and gas lines.
- HVAC Contractors: For installing heating, ventilation, and air conditioning systems.
b. Research and Gather Recommendations
Start by gathering a list of potential subcontractors. You can:
- Ask for Referrals: Consult other contractors, architects, or builders for recommendations on reliable subcontractors they’ve worked with.
- Use Online Directories: Platforms like Angi (formerly Angie’s List), HomeAdvisor, or Thumbtack allow you to find subcontractors based on location and reviews.
- Visit Trade Associations: Look into associations such as the National Electrical Contractors Association (NECA) or the Plumbing-Heating-Cooling Contractors Association (PHCC) for qualified subcontractors.
c. Initial Screening
Once you have a list of subcontractors, conduct an initial screening:
- Check Licenses and Certifications: Ensure they are licensed and certified to perform the specific work in your state.
- Verify Insurance: Subcontractors should carry liability insurance, and in most cases, worker’s compensation insurance. This protects you from liability if an accident happens on-site.
- Review Portfolio: Ask for samples of past projects similar to yours. Check if they have experience with ADU construction and have worked on similar-sized projects.
- Read Reviews: Look at customer reviews and ratings on sites like Google, Yelp, or the Better Business Bureau (BBB).
2. Vetting Subcontractors
a. Conduct Interviews
Once you’ve shortlisted potential subcontractors, schedule interviews. During the interview:
- Discuss Project Scope: Clearly explain the scope of work to ensure they understand the requirements.
- Request References: Ask for contact information of past clients and speak to them about their experience working with the subcontractor.
- Ask About Workload: Ensure the subcontractor has enough capacity to take on your project and meet the deadlines without compromising quality.
- Check Compliance: Ask about their familiarity with local building codes and inspection processes, especially for plumbing, electrical, and HVAC systems.
b. Evaluate Cost Estimates
Get detailed cost estimates from each subcontractor. The estimates should include:
- Labor Costs: Total cost of labor and how it’s broken down (hourly rates vs. fixed rate).
- Materials: Costs for materials they will need to procure.
- Timeline: A timeline for completing their part of the project.
- Contingency Plan: How they handle cost overruns or unexpected issues (e.g., unforeseen site conditions).
c. Verify Credentials
To ensure reliability, check the following:
- License Number: Verify the subcontractor’s license with the state’s licensing board to ensure it’s valid and up to date.
- Insurance Proof: Ask for proof of insurance and check the policy’s validity and coverage.
- Background Check: Depending on the size and scope of your project, you may want to conduct a background check on the company to ensure no legal disputes or financial issues.
3. Managing Subcontractors
a. Contracts and Documentation
Draft a clear and detailed contract with each subcontractor that outlines:
- Scope of Work: Clearly specify what tasks they are responsible for (e.g., installing all electrical outlets, fixtures, and wiring).
- Payment Terms: Define how payments will be made (e.g., milestone-based payments, lump sums, or hourly wages). Include conditions for withholding payments if work doesn’t meet expectations or inspections fail.
- Timeline: Include a clear schedule for when work will start, major milestones, and the completion date.
- Warranties: Define warranties for both labor and materials. It’s common for HVAC, plumbing, and electrical work to come with a one-year labor warranty.
- Termination Clauses: Include provisions for terminating the contract if the subcontractor fails to perform or meet the agreed-upon standards.
b. Communication and Coordination
Regular communication is key to managing multiple subcontractors:
- Project Manager: Appoint a project manager (or be your own) to oversee the subcontractors and ensure everyone is aligned with the overall project timeline.
- Site Meetings: Hold weekly site meetings with all key subcontractors to track progress, address challenges, and coordinate work to avoid scheduling conflicts (e.g., electricians and plumbers needing the same space).
- Progress Reports: Request weekly or bi-weekly progress updates to ensure that tasks are being completed on time.
- Online Tools: Use project management software such as Buildertrend, Procore, or CoConstruct to track project milestones, share documents, and communicate with subcontractors in real-time.
c. Inspections and Quality Control
Ensure that the work meets your standards and local building codes by:
- Scheduling Inspections: Coordinate with local authorities to schedule inspections at key stages (e.g., electrical rough-in, plumbing rough-in, HVAC duct installation). Do this before walls are closed up.
- Quality Checks: Regularly visit the site to check on the quality of work. Make sure all materials and workmanship meet the specified standards.
- Holdbacks for Quality: Hold back a portion of the payment until after final inspections are passed and any punch list items are addressed.
d. Payment and Finalization
- Progress Payments: Pay subcontractors in stages based on completed work, withhold a percentage (e.g., 10% retainage) until final inspection and punch list completion.
- Lien Waivers: Obtain signed lien waivers from subcontractors after each payment to protect yourself from any future claims related to unpaid work or materials.
4. Handling Disputes
Disputes can arise, so it’s essential to have a system in place for resolving them:
- Mediation First: Include a mediation clause in the contract. If a dispute arises, try to mediate and resolve issues before taking legal action.
- Document Everything: Keep detailed records of communications, progress reports, and payments to ensure you have evidence in case of disputes.
- Termination Clause: Have clear termination clauses for subcontractors who fail to meet contractual obligations.
Conclusion
Successfully managing subcontractors for specialized tasks like electrical, plumbing, and HVAC work requires thorough vetting, detailed contracts, ongoing communication, and regular quality checks. By establishing clear expectations, using project management tools, and monitoring progress closely, you can ensure that subcontractors deliver high-quality work on time and within budget.
Up next
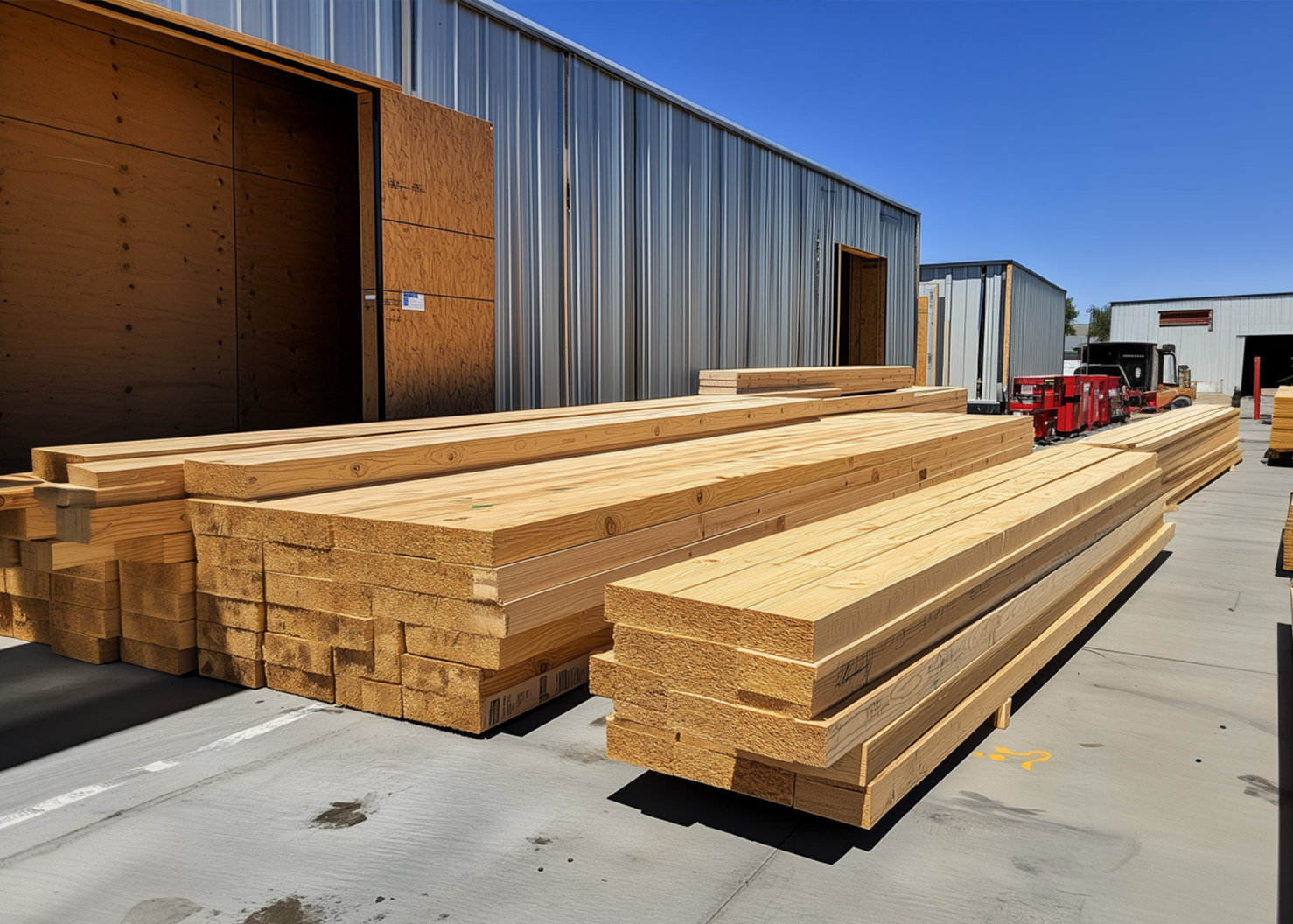