5.1.3 Exterior and Framing
After the foundation has cured, framing begins, where the structure of the ADU takes shape. Framing and exterior work are critical steps in the construction of an ADU (Accessory Dwelling Unit) as they establish the structure and ensure the building is weatherproof and stable. Here’s a detailed guide on the framing and exterior work process
Why It Matters
Framing and exterior work establish the structural integrity and weatherproofing of an ADU. Proper execution during this stage ensures durability, energy efficiency, and resistance to weather and environmental challenges.
Key Components
- Framing
- Purpose: Provides the ADU’s structural skeleton, supporting walls, windows, doors, and roofing.
- Process: Includes floor framing, wall framing (with openings for windows and doors), and roof framing using trusses or rafters.
- Materials: Commonly uses dimensional lumber or engineered wood for strength and durability.
- Best Practices: Ensure all framing is level, square, and secured to the foundation with anchor bolts and hurricane ties for stability.
- Exterior Sheathing
- Purpose: Adds rigidity and forms a base for siding and roofing materials.
- Materials: Plywood or OSB (Oriented Strand Board) for walls and roofs.
- Best Practices: Include weather-resistant barriers (WRBs) to protect against moisture while allowing internal vapor to escape.
- Windows and Doors
- Installation: Flashing, shims, and sealing ensure airtight and watertight openings.
- Energy Efficiency: Use insulated and weather-stripped options to improve energy performance.
- Roofing
- Materials: Options include asphalt shingles, metal, or tile, with underlayment for added water protection.
- Steps: Install from bottom to top for proper overlap and water runoff.
- Ventilation: Ridge or soffit vents prevent moisture buildup in the roof structure.
- Siding and Exterior Finishes
- Materials: Options include vinyl, fiber cement, or wood siding, depending on budget and aesthetics.
- Best Practices: Ensure proper flashing and sealing to prevent water infiltration and accommodate material expansion.
Cost Considerations
- Labor: Typically $4–$10 per square foot for framing, depending on complexity and region.
- Materials: Costs include lumber, fasteners, sheathing, and siding, with typical framing expenses ranging from $7,000 to $16,000 for a 1,000-square-foot ADU.
1. Framing Overview
Framing is the structural skeleton of the ADU, providing support for the roof, walls, windows, and doors. The framing process typically involves installing studs, joists, and rafters that shape the building and distribute its weight.
Steps in Framing:
- Laying the Floor System:some text
- If the ADU is on a raised foundation, start by framing the floor. This involves installing floor joists, which are supported by the foundation and create the base for the flooring.
- Floor joists are spaced according to the building code (typically 16-24 inches apart).
- Wall Framing:some text
- Once the floor system is in place, the walls are framed using studs, which are vertical framing members that create the walls' skeleton.
- Top Plates and Bottom Plates (horizontal boards) are secured to the studs, forming the structure for each wall.
- Openings for windows and doors are framed using headers (horizontal beams that carry the load above the opening) and sills.
- Walls are framed on the ground and then lifted into place, secured, and checked for plumb (vertical alignment).
- Roof Framing:some text
- The roof is framed using trusses or rafters. Trusses are prefabricated, engineered units that span across the structure, while rafters are custom-built on-site.
- Rafters or trusses are installed at regular intervals to support the roof's weight and provide the base for the roofing materials.
Framing Materials:
- Lumber: Common framing materials include dimensional lumber (such as 2x4s or 2x6s), depending on the load-bearing needs and local codes.
- Engineered Wood: Engineered beams, such as LVL (Laminated Veneer Lumber) or glulam, are often used for structural beams or large openings.
Best Practices for Framing:
- Level and Square: Ensure that all framing is level and square to avoid structural problems later. Use a level and plumb bob to check for alignment.
- Anchor Bolts: Secure the framing to the foundation with anchor bolts or hurricane ties to provide stability and resistance against wind and seismic activity.
- Shear Walls: If the ADU is in an earthquake-prone area, shear walls (walls reinforced with plywood or other rigid materials) are essential for providing lateral stability.
2. Exterior Sheathing
After the frame is complete, the next step is to apply exterior sheathing to the walls and roof, which adds strength to the structure and provides a base for the siding and roofing materials.
Wall Sheathing:
- Plywood or Oriented Strand Board (OSB) is commonly used for exterior wall sheathing. It’s attached to the studs to add rigidity to the frame.
- The sheathing is installed with gaps at the edges (typically 1/8 inch) to allow for expansion and contraction due to weather changes.
- Sheathing also serves as a base for insulation and waterproofing layers, creating a tight envelope for the building.
Roof Sheathing:
- Roof sheathing, typically plywood or OSB, is applied over the rafters or trusses to create the base for roofing materials.
- Proper spacing and fastening of roof sheathing ensure durability and support for the roofing system.
Best Practices for Sheathing:
- Fastening: Use nails or screws to fasten the sheathing according to the local building code (typically 6 inches on center at the edges and 12 inches on center in the field).
- Weather-Resistant Barriers (WRBs): Once sheathing is installed, cover the walls with a weather-resistant barrier (like house wrap) to protect against water infiltration while allowing moisture to escape from inside the building.
3. Exterior Doors and Windows
Windows and doors must be installed properly to prevent air and water leaks.
Window Installation:
- Windows are installed within the pre-framed openings, using flashing to create a watertight seal around the edges.
- Shims are used to ensure the window is level and square before securing it with nails or screws.
Door Installation:
- Exterior doors are installed similarly, with attention to flashing and sealing the edges to prevent water damage.
- Use insulated doors for improved energy efficiency, and ensure all doors are weather-stripped to seal out drafts.
Best Practices:
- Flashing: Properly install flashing tape or membranes around all window and door openings to prevent water intrusion.
- Air Sealing: After installation, apply caulk or spray foam around the edges of windows and doors to ensure an airtight seal.
4. Roofing
Roofing protects the ADU from weather and is a critical part of the building envelope.
Roofing Materials:
- Asphalt Shingles: Common in residential construction, asphalt shingles are cost-effective and durable, lasting about 20-30 years.
- Metal Roofing: More expensive but offers durability and longevity (lasting 40-70 years), with better resistance to wind, fire, and rain.
- Tile Roofing: Provides a distinctive aesthetic and excellent longevity, though it is more expensive and requires additional structural support due to its weight.
Roofing Steps:
- Underlayment: Install a roofing underlayment, such as felt paper or synthetic membranes, over the sheathing to provide an additional layer of water protection.
- Shingle or Tile Installation: Roofing materials are installed according to manufacturer specifications, starting from the bottom of the roof and working up to ensure proper overlap and water runoff.
- Flashing: Install flashing around roof penetrations (such as chimneys or vents) to prevent leaks.
Best Practices:
- Proper Ventilation: Install ridge vents, soffit vents, or other ventilation systems to allow for airflow in the attic or roof space, preventing moisture buildup and extending the life of the roofing materials.
5. Siding and Exterior Finishes
The final step in exterior work is applying the siding and finishing details that protect the building and give it its finished appearance.
Siding Materials:
- Vinyl Siding: Affordable and low-maintenance, vinyl siding is a popular choice for ADUs.
- Fiber Cement Siding: Durable and resistant to fire, pests, and moisture, fiber cement (e.g., James Hardie) offers longevity and a variety of aesthetic options.
- Wood Siding: Provides a natural aesthetic but requires regular maintenance (e.g., sealing or painting) to protect against weathering.
Installation Steps:
- Install siding over the WRB or house wrap, starting from the bottom and working upwards to ensure water drains properly.
- Leave space at the edges of the siding to allow for expansion and contraction.
- Install trim around windows, doors, and corners for a finished look.
Best Practices:
- Waterproofing: Ensure all siding is properly flashed and sealed to prevent water from getting behind the cladding.
- Expansion Gaps: Leave appropriate gaps in siding materials to accommodate thermal expansion, especially with materials like vinyl or wood.
Conclusion
Framing and exterior work are essential phases in ADU construction, forming the structure and protecting it from the elements. Proper execution during framing, sheathing, window/door installation, roofing, and siding will ensure the ADU is structurally sound, energy-efficient, and resistant to moisture and weather-related damage.
The cost of framing for an ADU or other small structure depends on several factors, including the size of the structure, materials used, labor rates, and regional differences. Below is a breakdown of framing costs based on common elements:
1. Labor Costs
Labor typically accounts for a significant portion of framing expenses. This includes the wages paid to carpenters and construction workers who build the frame.
- Average Labor Cost: Framing carpenters typically charge $4 to $10 per square foot of the framed area, depending on the complexity of the project and regional labor rates.some text
- In areas with higher labor costs (e.g., California or New York), prices might reach the upper end of this range.
- In lower-cost areas, you may find framing labor closer to $4 to $6 per square foot.
- Framing Contractor Cost: For larger or more complex projects, some contractors might charge by the hour, with hourly rates ranging from $30 to $85 per hour for framing labor, depending on the worker's skill level and location.
2. Material Costs
Framing materials include lumber, nails, screws, and connectors, which contribute to the overall cost. Here's a breakdown of the primary materials:
a. Lumber
Lumber is the largest material cost in framing. The type and amount of wood you use depends on the size of the structure and design complexity.
- Studs (2x4 or 2x6): A standard wood frame for residential structures typically uses 2x4s for non-load-bearing walls and 2x6s for exterior and load-bearing walls. Prices can vary based on the market, but as of recent pricing:some text
- 2x4 stud lumber costs about $2 to $5 per stud.
- 2x6 stud lumber costs about $5 to $10 per stud.
- For a typical 1,000-square-foot ADU, expect to spend approximately $3,000 to $5,000 on lumber for the frame.
b. Engineered Lumber
For certain sections, such as headers over windows and doors or long spans, engineered wood products like LVL beams (Laminated Veneer Lumber) are used, which are more expensive but offer greater strength.
- LVL Beams: Prices range from $3 to $7 per linear foot, depending on size and load-bearing capacity.
c. Fasteners and Hardware
Nails, screws, and brackets used to fasten framing members together are a smaller but necessary cost. Expect to spend $300 to $600 on fasteners and brackets for a typical ADU.
3. Sheathing
Sheathing (usually OSB or plywood) adds rigidity to the frame and provides a base for exterior cladding.
- Cost of Sheathing:some text
- OSB (Oriented Strand Board): Costs between $10 and $25 per sheet (4’x8’).
- Plywood: Slightly more expensive, ranging from $20 to $35 per sheet.
- For a 1,000-square-foot ADU, expect to use around 50-100 sheets, with a total cost of approximately $500 to $2,500, depending on the material used.
4. Waste and Miscellaneous
Waste and contingency for material overages or damage typically add 5-10% to the total framing material cost. Additionally, some regions may require higher-grade materials (e.g., pressure-treated wood for specific applications), which could further increase the cost.
Total Estimated Framing Cost
- Labor + Material Costs per Square Foot: Combined, you can expect framing costs to be around $7 to $16 per square foot for a standard ADU, depending on the complexity of the design, location, and material choices.some text
- For a 1,000-square-foot ADU, framing could range between $7,000 and $16,000, inclusive of materials and labor.
Additional Factors Affecting Framing Costs
- Building Complexity: The more complex the design (e.g., vaulted ceilings, irregular shapes), the more time and material it will take, driving up the cost.
- Location: Local market conditions, labor costs, and regional building requirements can significantly affect the overall framing cost.
- Permitting and Inspections: These are additional costs that should be considered in the total framing budget, although they are not part of the actual framing work.
Conclusion
Framing an ADU typically costs between $7,000 and $16,000 for a 1,000-square-foot unit, with labor, lumber, and materials such as sheathing making up the bulk of the cost. By selecting cost-effective materials like OSB sheathing and using standard framing sizes (e.g., 2x4 studs), you can manage the overall framing expenses effectively. Always account for regional variations, labor availability, and project complexity to refine your budget further.
Up next
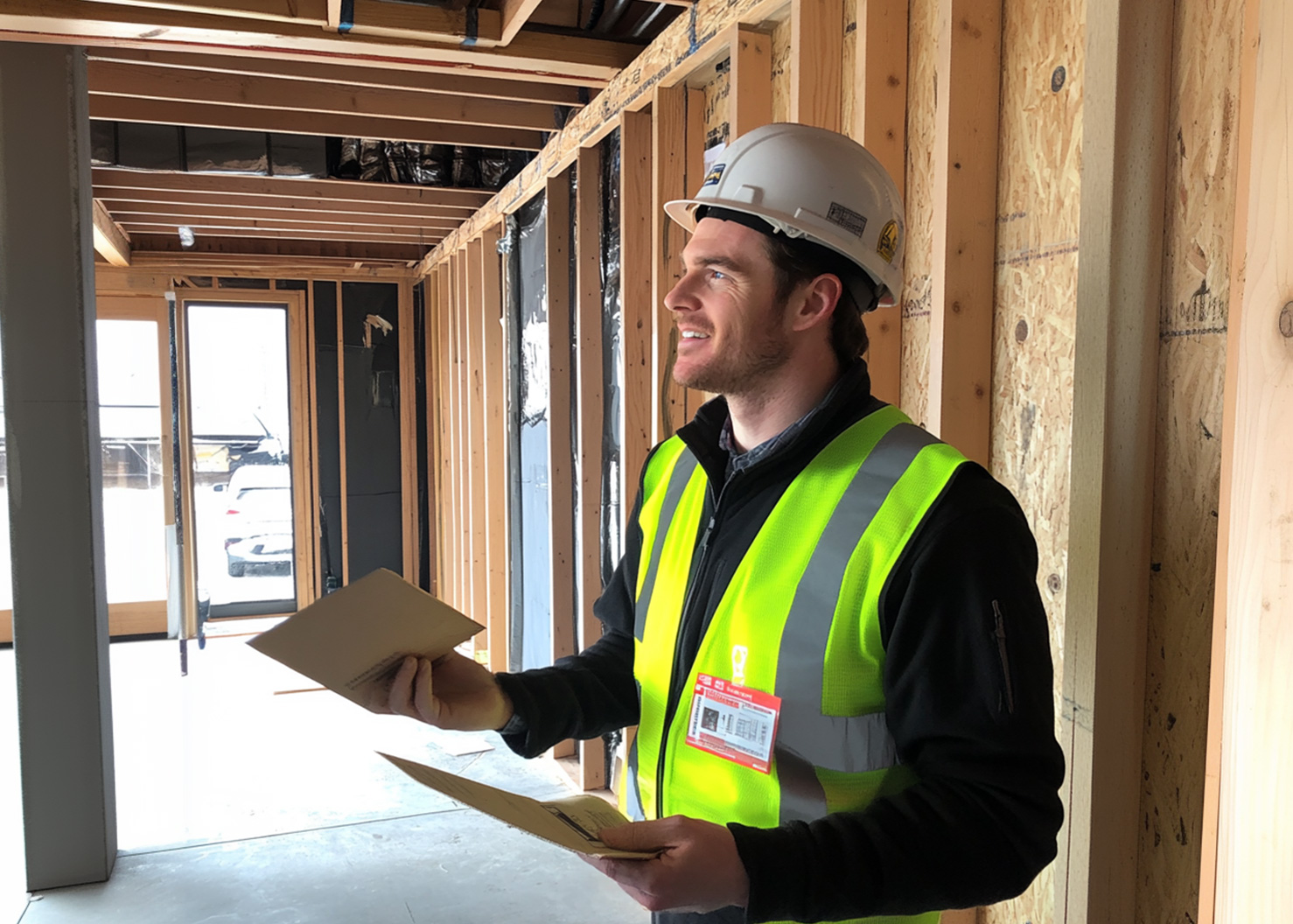