9.4 3D Printing and Modular Innovations
As the demand for ADUs (Accessory Dwelling Units) continues to rise, new technologies like 3D printing and modular construction are transforming how these units are built. These innovations offer faster build times, reduced costs, and enhanced sustainability, making ADUs more accessible and efficient. This guide explores how 3D printing and modular techniques can revolutionize ADU construction and improve project outcomes.
Why It Matters
3D printing and modular innovations are revolutionizing ADU construction by enhancing efficiency, reducing costs, and promoting sustainability. These cutting-edge technologies offer faster project timelines and high-quality builds, making them attractive options for modern housing solutions.
Key Components
- 3D Printing in ADU Construction
- What It Is: Uses advanced 3D printers to create structural components or entire ADUs layer by layer with materials like concrete or polymers.
- Benefits:
- Reduces material waste through precise manufacturing.
- Speeds up construction timelines.
- Lowers labor costs by minimizing manual intervention.
- Applications: Foundations, walls, or even fully printed ADUs in controlled environments.
- Modular Construction for ADUs
- What It Is: Prefabricates sections or modules of an ADU off-site in a factory-controlled setting, then assembles them on-site.
- Benefits:
- Shortens on-site construction time.
- Ensures consistent quality with factory-built components.
- Reduces on-site disruptions like noise and debris.
- Applications: Entire ADU units, bathroom pods, or kitchen modules.
- Combined Advantages
- Cost Savings: Both technologies optimize resource usage, reducing overall costs.
- Efficiency: Faster builds enable contractors to take on more projects.
- Design Flexibility: Modular units and 3D-printed components can be customized to meet client preferences.
- Sustainability: Lower material waste and energy consumption align with eco-friendly building practices.
- Challenges
- High Initial Costs: Requires significant investment in equipment and training.
- Regulatory Hurdles: Some regions may have building codes that don’t yet accommodate these technologies.
- Skill Gap: Requires specialized expertise to implement effectively.
- Future Potential
- Expanding accessibility as costs decrease and regulatory frameworks adapt.
- Innovations in materials and techniques could further enhance durability and efficiency.
- Potential for fully automated ADU production, reducing human error and costs.
Toolbox Ideas
- Cost Comparison Tool
- Evaluate the financial benefits of 3D printing or modular construction versus traditional methods.
1. Introduction to 3D Printing in Construction
What is 3D Printing in Construction?
3D printing in construction, also known as additive manufacturing, involves using computer-controlled machines to create structures layer by layer from materials like concrete, composites, and polymers. The technology is gaining traction in the ADU industry due to its potential to streamline the building process, reduce material waste, and cut costs.
Materials Used in 3D Printing for ADUs:
- Concrete: A common material for 3D-printed homes, providing durability and strength. It’s used in building walls, foundations, and structural components.
- Composites: These are lightweight, high-strength materials used for specialized components like insulation and internal walls.
- Plastics and Polymers: Used for non-structural elements, such as flooring and finishing touches.
How 3D Printing Works in ADU Construction:
- Design: Architects and engineers create a digital model of the ADU using CAD software. This model is converted into machine-readable instructions for the 3D printer.
- Layer-by-Layer Construction: The 3D printer builds the ADU by depositing layers of material, following the design exactly. This process is automated, significantly reducing human error.
- Finishing Touches: After the basic structure is printed, traditional construction methods are used to install plumbing, electrical, and interior finishes.
Benefits of 3D Printing in ADU Construction:
- Reduced Waste: The precision of 3D printing results in minimal material waste compared to traditional methods.
- Faster Build Times: 3D printers can build the basic structure of an ADU in a matter of days, reducing the overall construction timeline.
- Cost Savings: Fewer materials, less labor, and faster build times all contribute to reduced costs, making ADUs more affordable.
2. Modular Construction Techniques
What is Modular Construction?
Modular construction involves manufacturing sections (or modules) of a building in a factory and then assembling them on-site. Each module is constructed under controlled conditions, allowing for higher quality standards and faster assembly when transported to the building site.
How Modular Construction Works for ADUs:
- Factory Manufacturing: Modules are prefabricated in a factory setting, where the environment is controlled, allowing for consistent quality and efficiency.
- Transportation to the Site: Once the modules are completed, they are transported to the ADU’s location. The site is prepped with a foundation, utilities, and necessary connections.
- On-Site Assembly: The modules are then assembled on-site, often in a matter of days, to create a fully functional ADU. Interior finishes, utilities, and final touches are installed post-assembly.
Advantages of Modular Construction for ADUs:
- Speed: Since the modules are prefabricated, on-site construction time is drastically reduced. A modular ADU can be completed in weeks rather than months.
- Quality Control: Building in a controlled factory environment ensures that each module meets high standards and is protected from weather-related issues that can affect quality during traditional on-site construction.
- Cost Efficiency: Modular construction reduces labor costs, waste, and material costs by centralizing the building process. Bulk purchasing of materials in a factory setting can also lower overall project costs.
- Sustainability: The precision of modular construction minimizes waste, and building in a factory reduces the environmental impact of transportation and storage of materials.
3. Revolutionizing ADU Building with 3D Printing and Modular Construction
These emerging technologies offer significant benefits over traditional construction methods, revolutionizing the way ADUs are built and expanding the possibilities for builders, contractors, and homeowners.
a. Efficiency and Speed
- How It Helps: Both 3D printing and modular construction drastically reduce construction time. For example, 3D printing can create the shell of an ADU in a matter of days, while modular construction allows for simultaneous site preparation and off-site manufacturing, cutting total project timelines in half.
- Impact on ADU Industry:
- Faster builds mean more ADUs can be constructed in the same amount of time, helping to meet growing demand.
- Reduced timelines lead to lower labor costs and faster returns on investment for homeowners and developers.
b. Improved Sustainability
- How It Helps: 3D printing and modular construction reduce waste and optimize material usage, which makes them more environmentally friendly than traditional construction methods. With increasing focus on sustainability, these technologies offer a greener alternative for building ADUs.
- Impact on ADU Industry:
- ADUs built using these methods are more energy-efficient and eco-friendly, appealing to homeowners and renters who prioritize sustainability.
- Reduced waste and energy consumption during construction contribute to lower overall environmental impact.
c. Cost Reduction
- How It Helps: By minimizing waste, labor, and build time, both 3D printing and modular construction lead to significant cost savings. These technologies make ADUs more accessible to a wider audience, including budget-conscious homeowners and developers.
- Impact on ADU Industry:
- Lower costs make ADUs a more viable option for affordable housing and rental properties.
- More affordable ADUs expand the potential market for builders, enabling them to take on more projects.
While 3D printing and modular construction offer many benefits, such as reduced costs, faster build times, and improved sustainability, there are also several disadvantages and challenges associated with these types of housing, especially when it comes to permitting, financing, and overall market acceptance. Below is a comprehensive list of potential downfalls and cons of using 3D printing and modular construction in ADU projects.
1. Regulatory and Permitting Challenges
a. Unclear Building Codes and Regulations
- Challenge: Many local building codes and zoning regulations are not yet adapted to accommodate 3D-printed or modular homes. This can create uncertainty when applying for permits, as local authorities may not have the necessary experience or knowledge to approve these projects.
- Impact:
- Longer Permitting Process: Since these technologies are relatively new, the approval process may take longer as local governments and building departments may need to assess the safety and compliance of the structures.
- Variations by Region: Permitting requirements can vary significantly between regions, making it harder to standardize 3D-printed or modular ADUs.
b. Difficulty in Meeting Local Zoning Requirements
- Challenge: Zoning laws might restrict the use of certain construction methods, particularly in residential neighborhoods where traditional building methods are expected.
- Impact:
- Zoning Restrictions: Homeowners might face challenges when trying to build 3D-printed or modular ADUs in areas that prioritize conventional construction methods.
- Special Exemptions: In some cases, homeowners may need to apply for special exemptions or variances, which can be time-consuming and costly.
2. Financing and Insurance Issues
a. Limited Financing Options
- Challenge: Traditional lenders are often hesitant to finance 3D-printed or modular homes because these types of structures are not widely understood or accepted in the housing market. Many mortgage lenders prefer conventional construction due to the established track record of financing traditional homes.
- Impact:
- Difficulty Securing Loans: Homeowners may struggle to secure traditional mortgage financing for 3D-printed or modular ADUs, which can limit the accessibility of these types of homes for many people.
- Higher Interest Rates: If financing is available, it may come with higher interest rates due to the perceived risk associated with non-traditional construction methods.
b. Challenges with Home Insurance
- Challenge: Insurers may be reluctant to cover 3D-printed or modular homes due to a lack of historical data on how these structures hold up over time. Insurance companies may also have concerns about the durability, fire safety, or long-term performance of the materials used.
- Impact:
- Higher Insurance Premiums: Even if insurance is available, premiums for 3D-printed or modular homes may be higher compared to traditional homes, reflecting the perceived risk.
- Limited Coverage: Some insurers may provide only limited coverage or exclude certain elements of the home, such as structural components built with non-conventional materials.
3. Market Acceptance and Resale Value
a. Limited Resale Market
- Challenge: Since 3D-printed and modular homes are still relatively new, potential buyers may be unfamiliar with these construction methods, leading to skepticism about their long-term value and durability.
- Impact:
- Lower Resale Value: Homeowners may find it more difficult to sell a 3D-printed or modular home, especially if buyers are wary of purchasing non-traditional structures.
- Smaller Buyer Pool: There may be fewer potential buyers interested in purchasing a 3D-printed or modular ADU, which can limit demand and make it harder to resell.
b. Stigma Around Non-Traditional Construction
- Challenge: Some buyers and homeowners may still prefer traditional construction methods due to the perception that they are more durable and reliable.
- Impact:
- Perception of Lower Quality: Even though 3D-printed and modular homes can be built to high standards, there may still be a stigma that these homes are of lower quality than stick-built homes.
- Market Hesitation: Realtors and potential buyers may be hesitant to engage with 3D-printed or modular homes, slowing market acceptance.
4. Durability and Longevity Concerns
a. Unproven Long-Term Performance
- Challenge: While 3D printing and modular construction methods have shown promise, their long-term durability and resilience have not been fully tested in real-world conditions over several decades. This raises concerns about how these homes will perform over time.
- Impact:
- Unknown Lifespan: Unlike traditional homes, which have centuries of proven performance, 3D-printed and modular homes are relatively new, and there is limited data on how they will age, particularly under extreme weather conditions or other environmental factors.
- Potential Maintenance Issues: Homeowners may face unforeseen maintenance challenges as the materials used in 3D-printed or modular homes age.
b. Vulnerability to Natural Disasters
- Challenge: While modular homes are generally built to high standards, they can still be more vulnerable to certain natural disasters, such as high winds, earthquakes, or flooding, depending on the materials used and how the structure is anchored.
- Impact:
- Structural Concerns: In areas prone to natural disasters, modular and 3D-printed homes may need additional reinforcements to ensure they meet safety standards. This could lead to higher costs or make these homes less suitable for certain regions.
5. Limited Customization and Design Constraints
a. Design Limitations for 3D-Printed Homes
- Challenge: 3D printing technology currently has limitations when it comes to creating highly customized or complex designs. While it excels at creating simple, repetitive shapes, more intricate designs may be difficult or costly to execute.
- Impact:
- Less Architectural Flexibility: Homeowners who want unique or complex architectural designs may find 3D printing too limiting, as the technology is more suited to streamlined, minimalistic shapes.
- Higher Costs for Customization: Customized 3D-printed designs can be more expensive, offsetting some of the cost savings that come with 3D printing technology.
b. Modular Construction Standardization
- Challenge: While modular construction is efficient, it often relies on standardized designs to optimize factory production. This can limit the level of customization available to homeowners, particularly those who want a highly personalized ADU.
- Impact:
- Limited Design Options: Many modular homes follow a set design template, offering limited flexibility in layout and aesthetic choices. Homeowners seeking a unique, custom-built ADU may find modular construction too restrictive.
- Difficulty Modifying After Construction: Modular homes are often more difficult to modify after they’ve been assembled, meaning homeowners may have fewer options for future renovations or additions.
6. Logistics and Transportation Challenges
a. Transportation of Modular Units
- Challenge: Transporting large, pre-fabricated modules from the factory to the build site can present logistical challenges, especially in urban areas with narrow streets or remote locations that are hard to access.
- Impact:
- Additional Transportation Costs: Depending on the distance between the factory and the build site, transportation costs can add a significant expense to modular construction projects.
- Site Access Limitations: In some locations, transporting large modules may be impractical or impossible, limiting where modular ADUs can be built.
b. On-Site Assembly Requirements
- Challenge: Although modular homes are mostly prefabricated, they still require on-site assembly and finishing, which can sometimes result in delays if the site is not properly prepared or if there are weather-related challenges.
- Impact:
- Assembly Delays: Poor site preparation or unforeseen issues with utility hookups or foundations can lead to delays in the assembly process, which may offset some of the time saved by prefabricating the modules.
- Coordination with Local Contractors: Additional coordination with local contractors may be necessary for on-site assembly, leading to potential communication or scheduling issues.
Conclusion: Weighing the Pros and Cons
While 3D printing and modular construction offer exciting opportunities for transforming the ADU industry, it’s important to be aware of the potential challenges. Regulatory hurdles, financing and insurance difficulties, durability concerns, and market acceptance issues can create roadblocks for these technologies. However, as the industry evolves, solutions to many of these challenges are likely to emerge, making these innovations more accessible and viable in the future.
Key Takeaways:
- Regulatory Challenges: Building codes and permitting processes are not always adapted to 3D-printed and modular construction, leading to delays.
- Financing and Insurance Issues: Limited financing options and higher insurance premiums may make these homes less accessible.
- Durability Concerns: The long-term performance of these homes is still largely untested, which can raise questions about longevity and resale value.
- Market Acceptance: There may be stigma and a limited buyer pool for non-traditional homes, making it harder to resell these properties.
- Customization Constraints: 3D-printed and modular homes may offer less design flexibility compared to traditional construction.
- Logistical Hurdles: Transporting and assembling modular units can be complex, adding costs and potential delays.
By understanding these challenges, ADU entrepreneurs and contractors can better prepare for the hurdles that may arise when adopting 3D printing and modular construction technologies.
4. Case Studies and Examples
a. ICON’s 3D-Printed Homes
- Overview: ICON, a leader in 3D printing for construction, built one of the first 3D-printed homes in the U.S. in 2018. The company uses a proprietary concrete mix and large-scale 3D printers to create homes quickly and efficiently.
- Impact on ADUs: ICON has since expanded its technology to ADU construction. By printing the structural components of the ADU on-site, they reduce build times, costs, and material waste. Their 3D-printed ADUs are now being used as backyard units and affordable housing solutions in various parts of the U.S.
- Key Takeaway: ICON’s use of 3D printing has proven that the technology can be successfully applied to ADU construction, offering a scalable and sustainable solution for the housing crisis.
b. Boxabl’s Modular ADUs
- Overview: Boxabl is a company specializing in modular construction, offering pre-fabricated ADUs that are shipped to the build site and assembled in just a few hours. Their flagship product, the Casita, is a 375-square-foot modular ADU that includes a kitchen, bathroom, and living space.
- Impact on ADUs: Boxabl’s modular approach significantly reduces construction times and costs. The Casita can be transported and set up in a single day, making it an ideal solution for homeowners who want a quick, affordable ADU.
- Key Takeaway: Boxabl’s success in the modular ADU market highlights the efficiency and scalability of modular construction, making it a practical option for builders and homeowners alike.
c. Mighty Buildings’ Hybrid 3D-Printed and Modular ADUs
- Overview: Mighty Buildings is a California-based company that combines 3D printing with modular construction. They 3D-print the structural components of their ADUs and assemble the units off-site in a factory before transporting them to the build location.
- Impact on ADUs: By combining the precision of 3D printing with the efficiency of modular construction, Mighty Buildings has created an innovative approach to building ADUs. Their hybrid method reduces waste, lowers costs, and speeds up the construction process.
- Key Takeaway: Mighty Buildings showcases how combining 3D printing and modular techniques can result in highly efficient, sustainable, and cost-effective ADU solutions.
Conclusion: The Future of ADU Construction
3D printing and modular construction are poised to revolutionize the ADU industry by offering faster, more cost-effective, and sustainable building methods. As these technologies continue to evolve, they will open up new opportunities for builders, contractors, and homeowners, making ADUs more accessible and efficient.
Key Takeaways:
- 3D Printing: Offers reduced waste, faster build times, and cost savings by automating the construction process and using innovative materials.
- Modular Construction: Speeds up the building process by prefabricating modules off-site, improving quality control and reducing overall project costs.
- Industry Disruption: Both technologies have the potential to disrupt traditional ADU construction methods, offering more efficient, sustainable, and affordable options for homeowners and developers.
- Case Studies: Companies like ICON, Boxabl, and Mighty Buildings demonstrate the real-world impact of these technologies on ADU construction, showing how they can be applied to create scalable, sustainable housing solutions.
By adopting 3D printing and modular construction techniques, ADU businesses can stay ahead of the curve, improve project outcomes, and offer cutting-edge solutions to clients seeking innovative, future-ready homes.
Up next
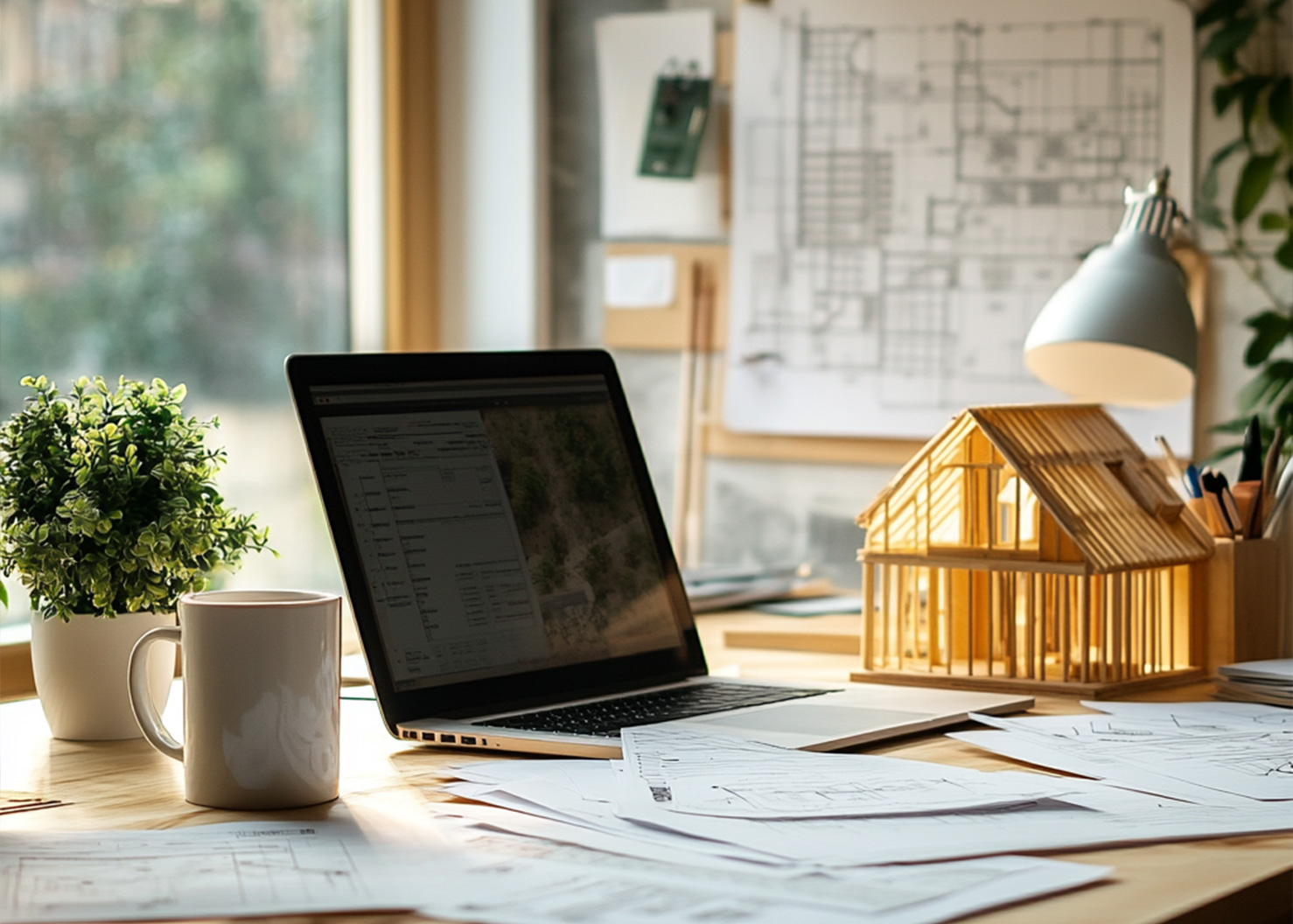